How do you keep track of goods moving in and out of your organization?
One of the most important documents in supply chain and inventory management is the goods receipt, a formal record that confirms the receipt of goods by an organization.
In this article, we’ll be diving deep into the importance of goods receipts. We’ll explore key benefits, discuss common challenges in goods receipt management, and best practices and strategies for better inventory management.
Definition of goods receipt
A good receipt is a document that confirms the receipt of goods by a company.
It is widely used in supply chain and inventory management to make sure that the goods that are delivered and received match the order specifications in terms of quantity, quality, and type. It acts as a formal acknowledgment from the receiving party that the goods have been delivered and comply with expectations.
Who issues a goods receipt?
Goods receipts are usually issued by the receiving party. Usually, it's the warehouse staff or procurement department of the company receiving the goods that creates it.
This takes place on the goods have been physically checked and verified.
What’s the difference between a goods receipt and an invoice?
Goods receipts and invoices are two important documents used in the purchasing process.
The main differences between the two documents are:
Key benefits of implementing a goods receipt process
Considering implementing a goods receipt process but not convinced of the need to do so?
Here are six key benefits you’ll see by issuing goods receipts:
- Improved inventory accuracy. Issuing goods receipts ensures that received goods match your purchase orders which helps to reduce discrepancies and prevent overstocking or stockouts.
- Streamline procurement workflow. Creating goods receipts facilitates better communication between procurement, warehouse, and accounting teams, and enhances efficiency by automating data entry and standardizing the process.
- Enhanced financial control. By using goods receipts, you’re linking purchase orders and invoices to actually received goods, ensuring you pay for what you receive.
- Improved quality insurance. The issuance of a good receipt comes after an inspection of goods upon arrival, which is an important process for identifying and resolving supplier issues promptly.
- Regulatory compliance. Using goods receipts gives you a detailed record of what materials enter your organization, supporting compliance with financial and legal regulations.
- Better supplier relationship management. Goods receipts facilitate communication and build trust through transparent, documented transactions. They also help you to monitor supplier performance based on delivery accuracy and quality.
How goods receipts contribute to supply chain efficiency
An efficient supply chain is critical for keeping costs low, reducing production slowdowns, and ensuring your ability to meet customer demand.
Here are a few important ways in which the use of goods receipts contributes to an efficient supply chain:
- Improved stock level accuracy
- Reduced wastage
- Enhanced ability to engage in demand planning
- More accurate and in-depth supplier performance monitoring
- Greater vendor accountability
- Integrated data entry and order fulfillment
- Quick identification of order discrepancies
- Streamlined returns
- More efficient resource allocation
- Avoidance of overpayments
- Strengthened collaboration and transparency across teams
- Reliable customer deliveries with few errors
- Audit trails to support regulatory compliance
Best practices for managing goods receipts
The typical business might process hundreds or even thousands of goods receipts a month, making a good system for managing them vital.
Here are some guidelines to implement to improve the management of goods receipts in your organization.
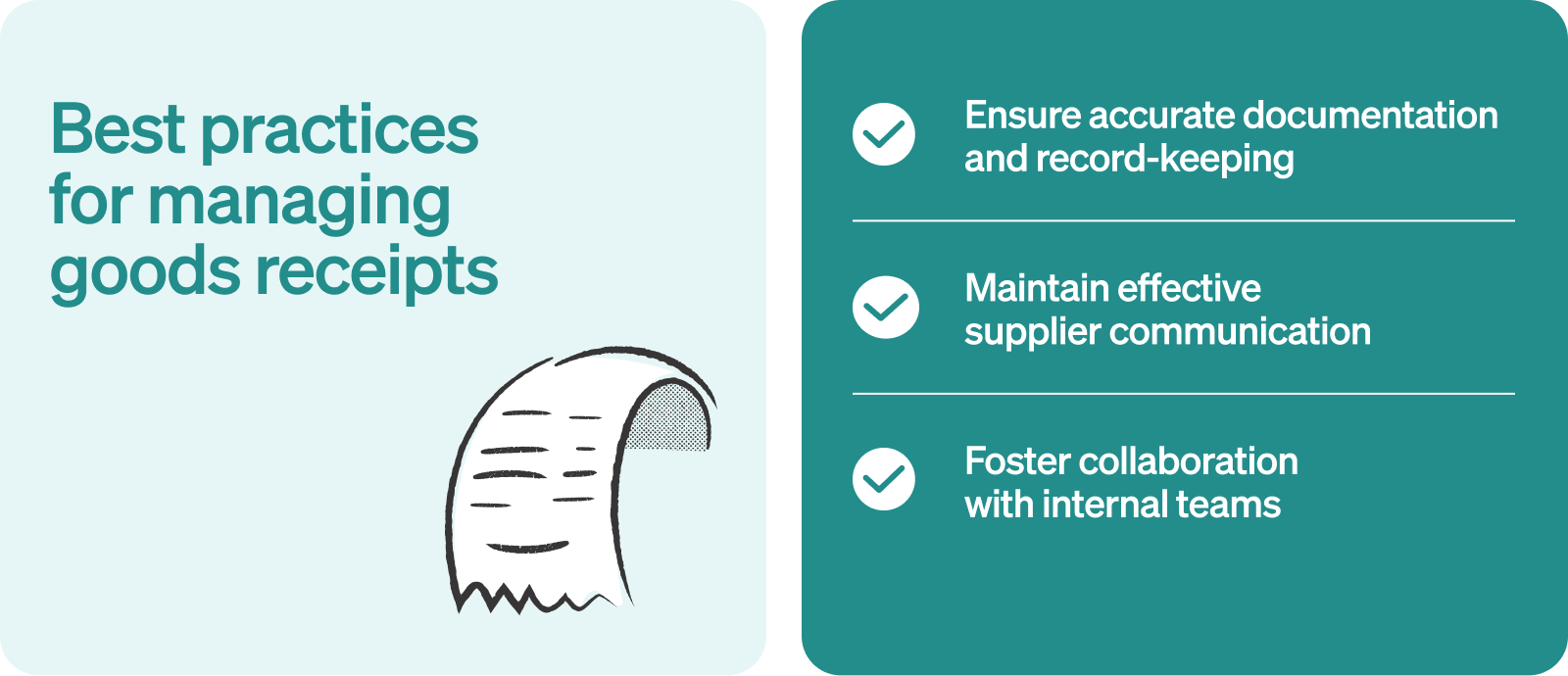
Ensure accurate documentation and record-keeping
Accuracy of documentation is critical.
Strategies to implement include:
- Verify purchase orders by cross-checking received goods against the PO to make sure they match
- Use software to automate data entry and maintain digital records of goods receipts to reduce manual errors
- Implement consistent templates for recording goods receipt details to standardize data entry
- Keep a well-organized history of goods receipts for easier audits and dispute resolution
Maintain effective communication with suppliers
Goods receipts can play an important role in improving supplier communication.
Some additional tips for managing effective communication with vendors include:
- Ensuring you set clear expectations and guidelines on delivery times, packaging, and documentation requirements
- Notifying suppliers promptly about discrepancies, damages, or other issues
- Maintaining supplier scorecards to make it easy to share evaluations with vendors
- Conducting periodic reviews with suppliers to discuss performance, issues, and opportunities for improvement
Foster collaboration with internal teams
Improving collaboration across the internal teams in your organization is an important part of goods receipt management.
You’ll need to:
- Define responsibilities for each team (procurement, warehouse, accounting)
- Use collaborative tools to notify relevant teams (like procurement and finance) when goods are received
- Connect goods receipt processes with finance, procurement, and inverter systems to enable seamless data sharing and minimize mistakes
Common challenges and solutions related to goods receipt management
Goods receipts may be a relatively simple solution, but that doesn’t mean they don’t come with their share of challenges.
Let’s explore some of the main ones you’re likely to experience, and some ideas on overcoming them.
Dealing with discrepancies between goods received and purchase orders
When the goods that are actually received don’t match what was ordered (such as incorrect items or quantities being delivered), processes get delayed, inventory errors occur, and disputes with suppliers can even take place.
Some solutions to this common issue include:
- Implementing a three-way matching process to compare the purchase order and goods receipt, and supplier invoice to identify and rectify discrepancies early
- Use barcode scanning or RFID technology to automate the verification process and reduce manual errors
- Established clear communication and discrepancy handling processes with your suppliers to strengthen the workflow if and when this happens
Addressing issues related to damaged or defective goods
On occasion, goods turn up damaged or even defective.
This can disrupt production schedules, cause financial losses, and even put a strain on supplier relationships.
Solutions here include:
- Establishing clear return and replacement policies in supplier contracts
- Ensuring that throughout inspections are completed upon receipt of goods with photos to document damages
- Implement preventative measures like using reliable shipping partners and implementing a packaging standard requirement with your vendors
Managing delays in goods receipt processing
Delays in recording the receipt of goods can lead to inventory inaccuracies, delayed payments, and mismatched records. It may even negatively impact your ability to claim for damages or incorrect deliveries with suppliers.
To reduce delays, you can:
- Invest in training staff on efficient receiving and recording processes
- Use a real-time inventory management system that automatically updates records
- Ensure you’re allocating sufficient resources, including personal and equipment
- Establish good communication practices with suppliers so you know when to expect large shipments and can make sure you’ve got staff and space to deal with incoming goods
Handling mismatched or missing documentation
One of the biggest issues that cause delays is when documentation is missing or incorrect.
You can prevent this from happening in the first place by:
- Requiring suppliers to provide advanced shipping notices (ASNs)
- Using document management systems to store and track relevant records
- Set up alerts and follow-ups to address missing documentation proactively
Implementing strategies to prevent inventory shrinkage
Inventory shrinkage can have a major impact on profitability and even harm the customer experience when orders cannot be fulfilled.
Let’s dive into some powerful strategies to mitigate the risk of inventory shortage.
Conduct regular audits and cycle counts
By performing frequent inventory checks, you’ll identify discrepancies early, allowing you to quickly update inventory counts and keep records accurate.
Establish clear security measures
Control access to inventory storage areas to prevent loss by theft or breakages. You can implement restricted entry protocols such as ID card access or sign-in sheets.
Train employees on inventory management best practices
Make sure employees have access to regular training on property inventory handling, storage, and recording protocols.
Use inventory management software
Get out of spreadsheets and start tracking inventory levels in real time with an inventory tracking system.
These powerful tools help improve visibility of stock movements and can even automatically flag discrepancies as they arise.
Streamline goods receipt through automation and technology
One of the most important technologies you can also implement is invoice matching.
A three-way invoice matching protocol requires that the supplier invoice, goods receipt, and original purchase order document all match up. This helps you to ensure that what you order, receive, and pay for are all the same.
BILL’s powerful accounts payable automation solution has built-in invoice matching to help you speed up the goods receipt process and reduce errors associated with manual data entry.
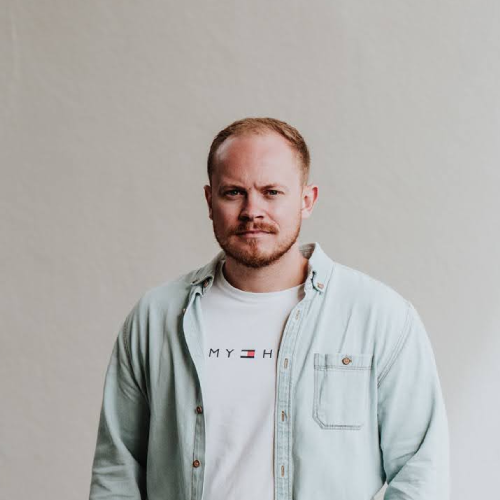